Improving energy efficiency in pet food manufacturing
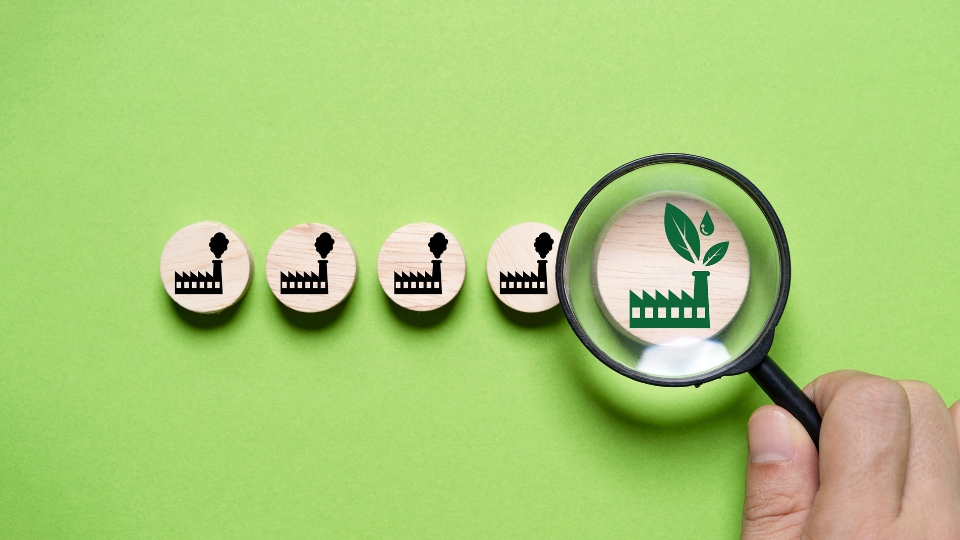
Production plants have a wide range of solutions at their disposal – old and new – to help them reduce their energy consumption. Which measures are most effective and what areas should they prioritize?
Whether driven by sustainability and corporate social responsibility (CSR) goals or by cost considerations, today’s pet food manufacturers are increasingly looking for ways to advance their energy efficiency.
We asked a number of processing experts to share insights into the steps that can be taken and the associated gains.
The attraction of solar panels
When animal health and nutrition company Alltech Serdán installed solar panels at its production plant in Mexico in 2022, the move was not intended to reduce costs or improve energy efficiency.
Instead, it was motivated by sustainability and CSR. These themes are baked into the plant’s workplace culture because, among other ingredients used in pet food, the company makes a plant-based extract that reduces emissions from livestock waste.
Therefore, installing solar panels to reduce the plant’s carbon footprint seemed like a natural fit, according to Marco Sanchez, Maintenance and Projects Manager at Alltech Serdán.
But of all the measures the plant has taken to reduce its energy costs in recent years, the solar panels have to date generated more cost savings than all but one other project, says Sanchez, who describes it as “a happy side effect”.
However, this does not mean that a pet food company must invest in flashy projects like solar panels or expensive equipment retrofits to make major strides in energy efficiency.
Companies can realize significant gains by tweaking key aspects of their existing processes – especially drying and preconditioning, according to Sajid Alavi, a professor specializing in extrusion processing at Kansas State University.
Anders Haubjerg, Process Engineer at equipment manufacturer Wenger, agrees. “Reducing the carbon footprint and decreasing energy consumption in extrusion and drying processes is a real goal that we often discuss with customers, as this can have a tangible payback in sustainability that can also lead to improved profitability of operations,” he comments.
Focus on the dryer
For pet food companies looking to cut back on energy costs, Alavi recommends starting with the dryer.
“Drying is a big energy-consumptive process, and if we can make drying more efficient, that saves on energy and improves overall sustainability,” he states.
Within the dyer, the first issue to consider is variability in the product’s final moisture content.
According to Alavi, manufacturers sometimes set their dryers to compensate for variability in the finished product.
For example, if a particular dryer tends to have a 2% margin of error and the goal is a finished product with a 5% moisture content, they may aim to dry to 3% or less to compensate.
Alavi explains how reducing dryer variability by even a single percentage point could allow manufacturers to increase their target moisture content from 3% to 4%, which could significantly reduce energy use.
Smaller adjustments
Updating old heating components, adding heat exchangers and even introducing new alternative fuels can reduce dryer energy consumption by 20-60%, according to Haubjerg, but retrofitting or replacing a dryer can come with significant costs.
But he emphasizes that it’s possible for manufacturers to save energy with smaller tweaks as well and that modifications which recapture energy from the dryer exhaust air, for example, can cut energy use by 10% or more, at a more moderate cost.
Subsequently, additional modifications can be made over time in a phased approach to achieve greater gains.
While Haubjerg agrees that the dryer should be the primary area of focus given its relatively high energy use, he recommends that manufacturers also consider the extruder technology they have in place as extruders can have different requirements when it comes to the kind of energy they use.
He suggests that manufacturers may want to consider options that not only maximize energy efficiency, but also offer a greater range of flexibility with respect to fuel choices in the future.
Installing solar panels and an economizer on the boiler at the Alltech Serdán plant have cut costs by some 30% in recent years.
However, Sanchez points out that the biggest cost savings have come from the decision to switch from using liquefied petroleum gas to compressed natural gas as the primary source of fuel.
How to avoid losing steam
Companies that have already begun work to optimize dryer efficiency should consider the use of steam in their preconditioner as a logical next step, according to Alavi.
Like drying, he says, creating steam is an energy-intensive process, and so manufacturers want to be sure that the steam they produce is applied evenly to the target ingredients with minimal loss of steam to the environment.
Current solutions to steam loss in the preconditioning process focus on designing systems to give the steam more opportunity to condense and ensure that ingredients are evenly exposed to the vapor.
But there is also emerging research – including studies in the works by Alavi’s team – exploring cutting-edge technologies to capture and recirculate steam that would otherwise be lost.
Ingredient selection
Another frontier for companies looking to take energy efficiency to the next level is ingredient selection, says Alavi. Some materials – corn or rice, for example – may better absorb steam in preconditioning than others.
This of course would have to be balanced with cost and ingredient availability and so the impact of ingredient selection may vary from one plant to the next. Alavi confirms this is another current area of research at Kansas State University.
And then there are options like solar panels and other forms of renewable energy.
While Alltech Serdán’s installation currently generates about 46% of the electricity it uses, the plant has set a goal to expand its solar farm and eventually supply 100% of its own electricity, according to Sanchez.
Financial incentives
Alavi notes that these kinds of projects may be particularly attractive to plants that may be eligible for government tax rebates or other incentives for solar panels or renewable energy projects, but they may not be the only way to qualify.
Companies may also qualify for certain energy use incentives if they have data on hand to show how their operations have or could be improved, he says.
“If you can show that one process is more energy efficient than the other, I think it’s worthwhile [collecting data] for anything that might give you some support. If you’re buying new equipment, a little help would go a long way,” he concludes.